About Us
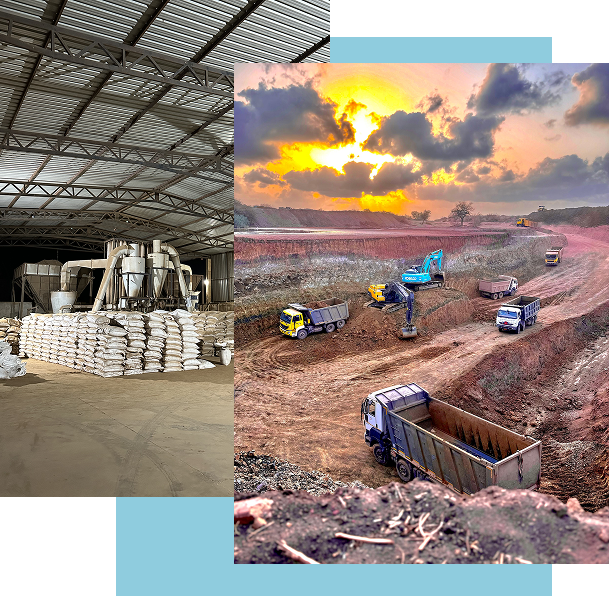
01
Our Story
M/s. Rameshwar Minechem is a prominent player in the export-import sector, boasting ownership of mines in Taluka Abdasa, located in Kutch District. Our state-of-the-art processing and grinding units are strategically positioned in the G.I.D.C. area of Taluka Mandvi, near Village Durgapur, ensuring seamless operations.
We pride ourselves on maintaining a cutting-edge laboratory for rigorous sample testing at every stage of production. This commitment ensures our valued clients receive materials of consistent, high-quality. Our processing unit's prime location facilitates efficient access to our mines and responsible distribution of finished products across the country and for export via Gujarat Adani Port and Kandla Port, situated 50 km and 120 km away, respectively.
Spanning 30 hectares, our operations are well-equipped with a skilled workforce and advanced mining equipment, including R.C.C. Silo, Bucket Elevator, Service Silos, Pulverizers, Dust Collectors, Pockland-Hitachi, Spraying Equipment, and Tractors. This extensive infrastructure underpins our capability to meet market demands with precision and efficiency.
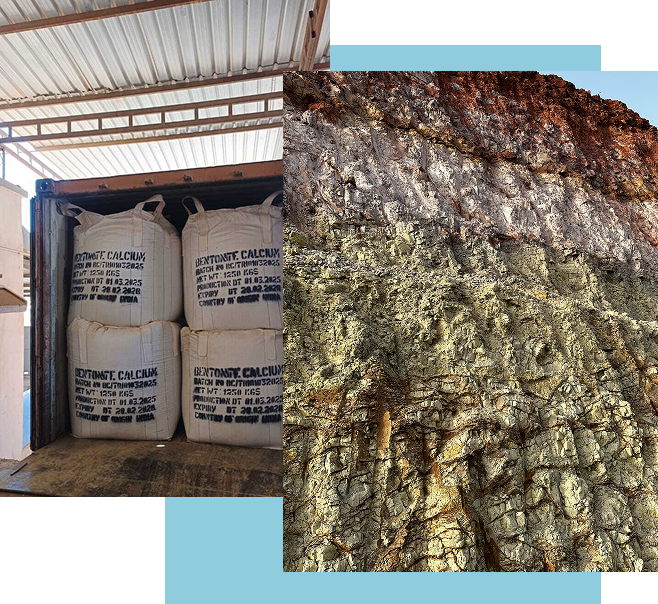
02
Bentonite Mining and Processing for Superior Quality: Layer by Layer Precision
Our bentonite mining operations utilize an open-cast method, acknowledging the inherent variability of this unique clay mineral. Formed through geothermal activity, bentonite quality naturally differs even within the same mine, influenced by the presence of various metal ions in the soil. This necessitates meticulous bentonite mining practices, including regular sampling and segregated storage of different grades to meet diverse quality requirements.
Sun Drying and Quality Control:
After excavation, the raw bentonite undergoes sun drying in open plots to achieve the optimal moisture content. This crucial step is followed by rigorous quality checks before the material is transported to our state-of-the-art processing facility.
Bentonite Activation for Enhanced Performance:
Recognizing the impact of mineral and metallic impurities, we employ a carefully controlled bentonite activation process at our factory. This crucial step enhances the inherent qualities of the bentonite under the strict supervision of our experienced team. Achieving the desired activation level and moisture content prepares the bentonite for the next stage.
Size Reduction and Custom Packaging:
The activated bentonite is then subjected to precise size reduction using our five-roller grinding system. This allows us to produce bentonite powder with a specific mesh size tailored to our buyers' exact specifications. Finally, the processed bentonite is packaged according to individual customer requirements.
Uncompromising Quality Assurance through Rigorous Testing:
Quality is paramount throughout our entire process, from the mine to the finished product. Our fully equipped laboratory conducts comprehensive testing at every stage, adhering to all parameters set by our clients. This continuous monitoring during processing and grinding ensures a consistently high-quality bentonite product.
Key Bentonite Properties and Applications:
Our extensive testing evaluates critical properties such as absorption capacity, gelling capacity, and the amount of active clay present. For instance, swelling capacity indicates absorption potential, while gel formation time and gel index reflect both absorption and viscosity. The M.B. value specifically quantifies the active clay content in the mineral bentonite.
Due to its exceptional high gel formation capacity and viscosity, our processed bentonite is widely utilized in key industries, including foundry industries and oil well drilling.
Plant |
Annual Capacity |
---|---|
Production Capacity |
35,000 MTS |
Raw Material Activation Capacity |
85,000 MTS |
Raw Material Storage Capacity |
20,000 MTS |
Finished Goods Storage Capacity |
1000 MTS |